KI-basierte optische Qualitätssicherung
Künstliche Intelligenz (KI) bei einem traditionsreichen Autozulieferer? Dass das geht, zeigt das Green-AI Hub Pilotprojekt mit der KÖSTLER GmbH aus Annaberg-Buchholz in Sachsen. Das Unternehmen verarbeitet unter anderem Textilien für Airbags. Die Qualitätssicherung im Produktionsprozess dieser Textilien erfolgt noch manuell, was monoton ist und Ausschuss erzeugt. Mithilfe von KI entwickeln wir eine automatisierte Qualitätsprüfung der Stoffe.
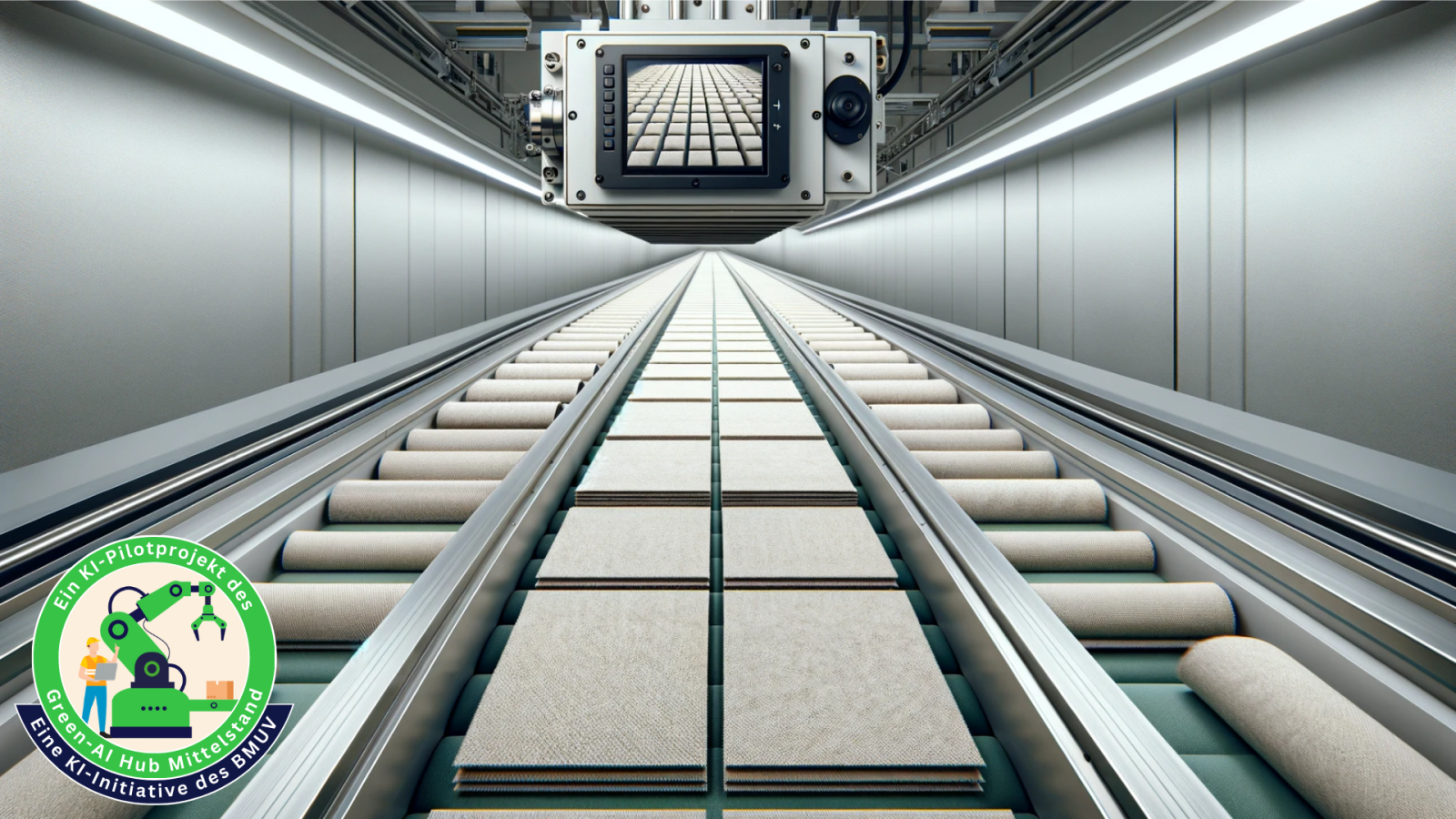
Die KÖSTLER GmbH: Ein Automobilzulieferer mit Geschichte
Die Firma KÖSTLER ist ein 1891 von Johann Köstler in Graslitz gegründetes Familienunternehmen. Ursprünglich war das Unternehmen im Bau von Musikinstrumenten und Zubehör tätig. Nach 1945 wurde das Unternehmen in Nauheim fortgeführt und erweiterte 1963 sein Geschäftsfeld auf die Automobilindustrie. Mit über 50 Jahren Erfahrung ist KÖSTLER heute ein führender Hersteller von Airbag-Scharnieren aus textilem Gewebe. Die Standorte befinden sich in Annaberg-Buchholz und Chomutov, Tschechien. KÖSTLER produziert Interieur-Teile wie Armauflagen und Sonnenblenden.
Herausforderung: steigende Qualitätsanforderungen
Wie andere Firmen aus dem Mittelstand steht auch die Firma KÖSTLER vor der Herausforderung des Fachkräftemangels. Dieser erschwert die Rekrutierung qualifizierter Mitarbeiter*innen, was die Produktionskapazitäten und Innovationsfähigkeit beeinträchtigt. Gleichzeitig haben sich die Anforderungen an die Automobilindustrie erheblich gesteigert. Endkund*innen erwarten höchste Qualität, Prozesssicherheit und Effizienz, es gibt strengere Standards für die Qualität und Zuverlässigkeit von Produkten und Dienstleistungen (IATF 16949 Standards). Hinzu kommen wachsende Erwartungen an nachhaltige und innovative Materialien, insbesondere im Bereich Leichtbau. All dies erfordert ständige Anpassungen sowie Investitionen in Personalentwicklung und technologische Fortschritte. Dies umfasst auch die Qualitätssicherung.
KÖSTLER setzt auf eine traditionelle Handarbeit und moderner Fertigungstechniken. Viele Prozesse erfolgen per Hand, was eine hohe Präzision und Sorgfalt garantiert. Zum Beispiel werden Textilnetze aufwendig zu Scharnieren vernäht. Produkte können so sehr gut an spezifische Kundenanforderungen angepasst werden. Nach der Fertigstellung werden die Scharniere verkauft und in weiteren Produktionsschritten verarbeitet, zum Beispiel durch das Einspritzen in Kunststoffteile. Dieser Prozess ermöglicht die Integration der textilen Scharniere in komplexe Bauteile, die in der Automobilindustrie und anderen Bereichen verwendet werden.
Verbesserte Qualitätssicherung durch Künstliche Intelligenz
Das KI-Pilotprojekt mit KÖSTLER setzt auf KI zur Qualitätssicherung der geschnittenen textilen Netze. Dazu wird eine innovative Prüfstation entwickelt, welche die Textilien automatisch nach Anforderungen in gut und schlecht sortiert.
Die Prüfstation nutzt KI-gestützte Bildverarbeitung und maschinelles Lernen, um die Textilien präzise zu bewerten. Die automatisierte Sortierung gewährleistet eine hohe Qualität der Produkte und reduziert fehlerhafte Teile.
Dies entlastet die Mitarbeitenden zugleich von monotoner Arbeit und ermöglicht es ihnen, sich auf anspruchsvollere Aufgaben zu konzentrieren, da weniger Personal für die Qualitätskontrolle benötigt wird. Die KI-gestützte Prüfstation verbessert die Effizienz und Qualität der Produktion. Langfristig stärkt dies die Wettbewerbsfähigkeit des Unternehmens und unterstützt nachhaltiges Wachstum.
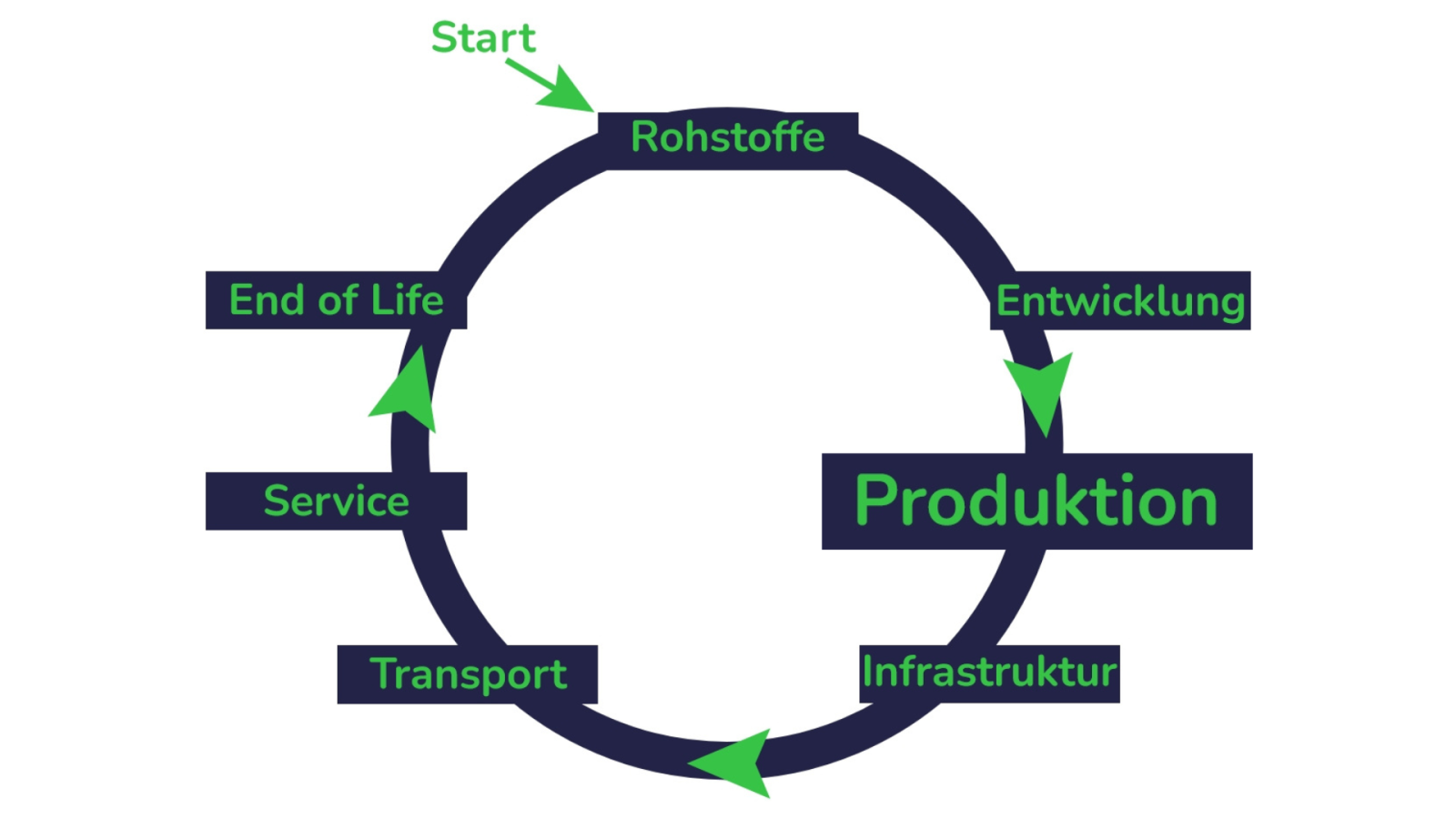
Ressourceneffizienz durch KI
KÖSTLER setzt durch das KI-Pilotprojekt mit dem Green-AI Hub Mittelstand auf KI, um die Ressourceneffizienz zu steigern und erhebliche Einsparungen zu erzielen. Die KI-basierte Qualitätsprüfung ist präziser und konsistenter als die menschliche Qualitätsprüfung. Das verringert voraussichtlich die Ausschussquote.
Ein weiterer Vorteil ist die frühzeitige Erkennung von Fehlertrends. Durch die kontinuierliche Überwachung und Analyse der Produktionsdaten kann die KI Abweichungen und Muster schnell identifizieren, dies ermöglicht eine sofortige Korrektur beim Schneiden der textilen Netze. Aktuell werden pro Design zwei Schablonen aus Kunststoff und Metall für die Qualitätsprüfung gefertigt. Durch die Implementierung der KI-gestützten Prüfstation kann der Bedarf dieser Schablonen um 50 Prozent auf eine reduziert werden.
Darüber hinaus wird der Platz- und Heizbedarf der großen Räumlichkeiten, die derzeit für die manuelle Qualitätskontrolle genutzt werden, reduziert. Die automatisierte Prüfstation benötigt weniger Platz und Energie, was die Betriebskosten senkt und die Ressourceneffizienz weiter steigert.
Vorstellung des Green-AI Hub-Pilotprojekts „KI-basierte optische Qualitätssicherung“ - 5:38 min.
-
Sven Pultar, Deutsches Forschungszentrum für Künstliche Intelligenz GmbH
Technologie
Fähigkeit der KI: Datenanalyse und Bilderkennung
KI-Modell: KI-gestützte Bildverarbeitung und maschinelles Lernen
Wertschöpfung
Phase: Qualitätskontrolle
Ziel der KI: Automatisierung manueller Prozesse zur Qualitätsprüfung
Ressourceneffizienz
Niedrigere Ausschussquote sowie Einsparungen bei den Betriebskosten sowie beim Material in der Produktion