KI-basierte Optimierung der Drehteileproduktion
HEISMANN Drehtechnik ist ein Hersteller von Präzisionsdrehteilen dessen zentrale Herausforderung darin besteht, die automatisierten Produktionsprozesse so zu gestalten, dass Prozessstabilität im Regelbetrieb gewährleistet bleibt. Produktionsunterbrechungen und -störungen, welche beispielsweise durch Materialschwankungen entstehen, erfordern umfangreiche Nachregulierungen durch Mitarbeitende und führen zu Ausschuss. Das Ziel des gemeinsamen KI-Pilotprojekts ist es, durch frühzeitige Fehlererkennung und optimierte Nachjustierung den Ausschuss zu reduzieren sowie personelle Ressourcen einzusparen.
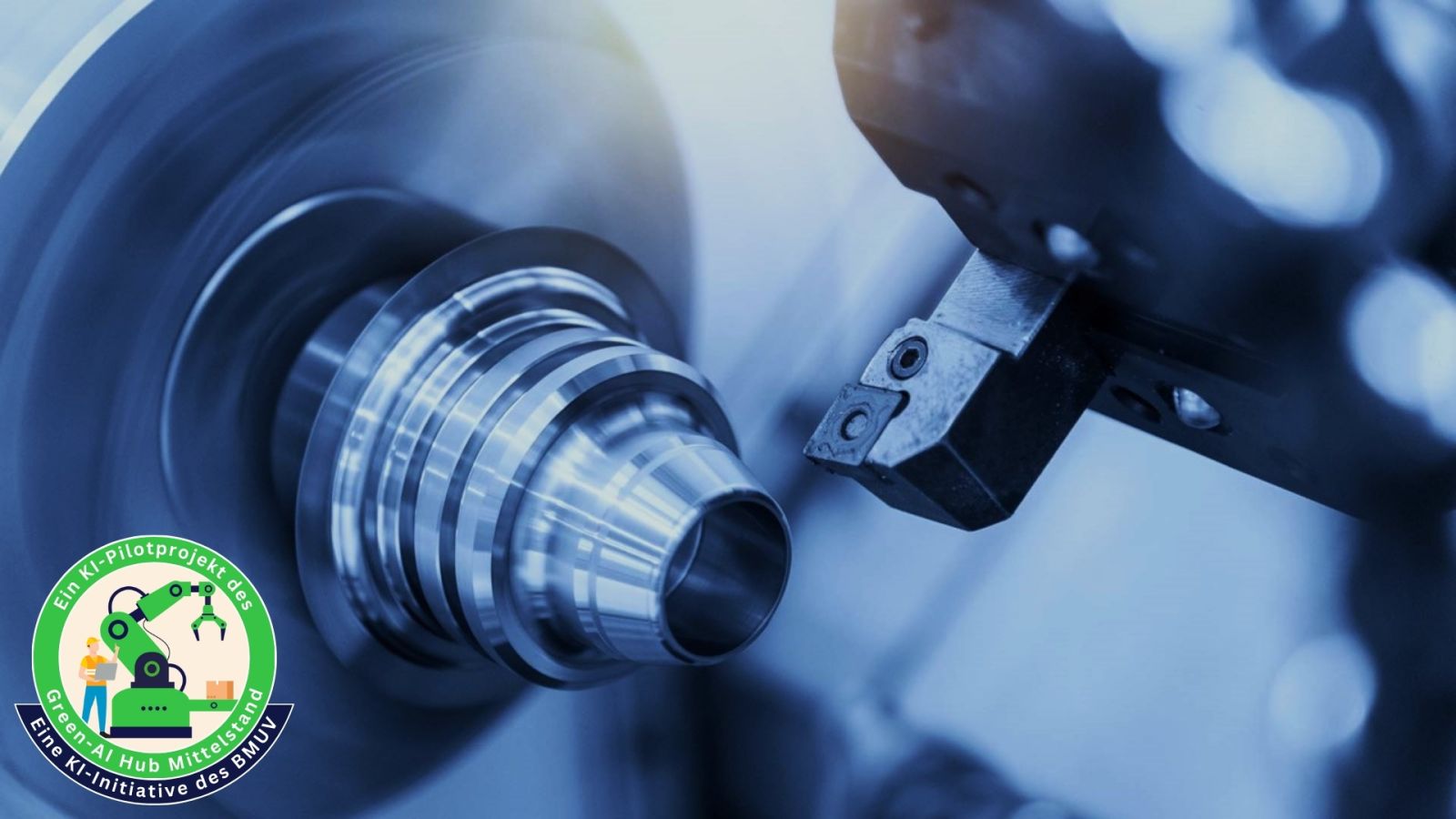
Präzisionsdrehteile aus dem Niederbergischen Land
HEISMANN Drehtechnik wurde 1918 gegründet und zählt heute mit 135 Mitarbeitenden zu den etablierten Herstellern von Präzisionsdrehteilen. Mit einem hochmodernen Maschinenpark mit 27 CNC-Mehrspindeldrehautomaten und sieben CNC-Drehfräszentren werden Präzisionsdrehteile aus verschiedenen Materialien wie Stahl, Messing, Aluminium und Kupfer hergestellt.
Herausforderungen: Reduzierung von Produktionsstörungen bei der Herstellung von Präzisionsdrehteilen
Produktionsunterbrechungen und Störungen führen dazu, dass der Prozess immer wieder nachgeregelt werden muss. Die Produktion von Ausschuss ist in diesem Fall deutlich wahrscheinlicher und teilweise sogar unvermeidbar. Um solche Produktionsstörungen und -unterbrechungen bestmöglich zu vermeiden, müssen die Mitarbeitenden den Prozess kontinuierlich überwachen und anpassen. Eine zentrale Stellgröße ist hierbei die manuelle Werkzeugkorrektur. Die dafür notwendigen Anpassungen sind abhängig von zahlreichen Einflussfaktoren. Viele dieser Faktoren sind für die Mitarbeitenden jedoch nicht transparent und ihre Auswirkungen auf die Stabilität des Prozesses lassen sich nur schwer vorhersagen.
Frühzeitige Erkennung von Fehlern und optimierte Nachjustierung durch Künstlicher Intelligenz
Das Ziel des KI-Pilotprojektes besteht darin, mithilfe einer frühzeitigen Erkennung und einer optimierten Nachjustierung die Ausschussquote zu reduzieren. Aufgrund der Vielzahl an Einflussfaktoren (Material, Temperatur, Werkzeuge usw.) und der eingeschränkten Transparenz, stößt die manuelle Nachjustierung durch die Mitarbeitenden an ihre Grenzen. Hier kann die Fähigkeit von KI, große Datenmengen zu analysieren, gewinnbringend eingesetzt werden. Die Reduzierung des prozessbedingten Ausschusses durch das KI-Pilotprojekt führt zu einer erheblichen Steigerung der Ressourceneffizienz. Die Künstliche Intelligenz ermöglicht es, frühzeitig mehr Informationen zu verarbeiten und die daraus gewonnenen Erkenntnisse mitarbeiterübergreifend in Form von Handlungsempfehlungen bereitzustellen. So können Mitarbeitende schneller und effektiver auf Veränderungen und Störungen im Prozess reagieren. Für diese Wahrscheinlichkeitsvorhersage von Fehlern und die Generierung der Handlungsempfehlungen für die Achseneinstellungen der Maschinen sowie der Vorhersage der Werkzeugstandzeit kommen Machine Learning (ML)-Algorithmen und kleinere neuronale Netze zum Einsatz.
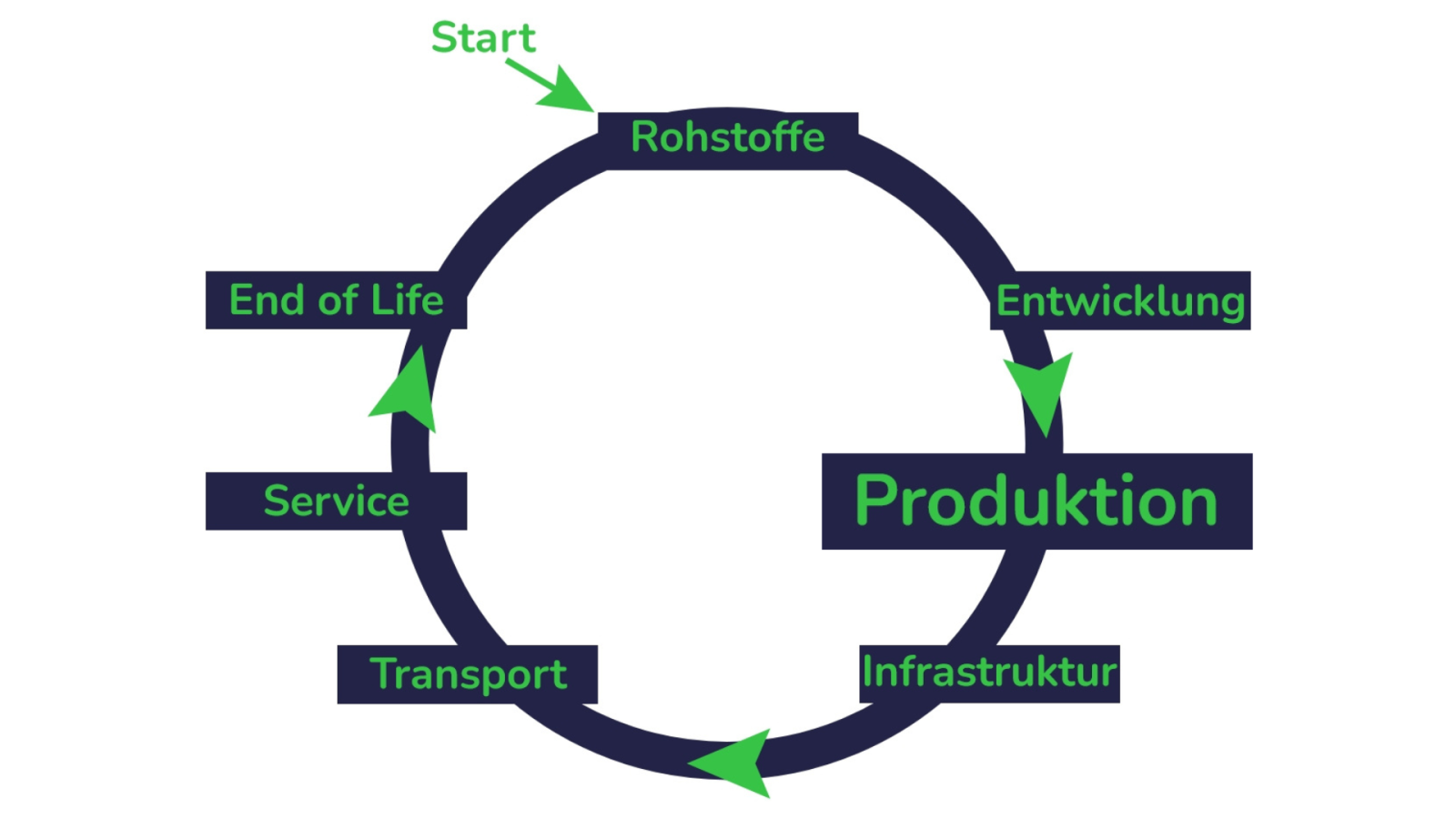
Ressourceneinsparung durch KI-basierte Prozessoptimierung
Durch den Einsatz einer KI-Lösung wird die Arbeit der Mitarbeitenden vereinfacht, da diese bisher oft auf ihre Erfahrung und Augenmaß zurückgreifen mussten, um den Produktionsprozess zu steuern. Mithilfe der KI können sie fundiertere Entscheidungen treffen, die den Herstellungsprozess sicherer gestalten. Somit wird das Unternehmen wettbewerbsfähiger, da es seltener zu Qualitätsmängeln und Reklamationen kommt, welche besonders bei hochpräzisen Drehteilen nicht tolerierbar sind. Ebenfalls hilft die KI-Lösung den Arbeitsaufwand in der Qualitätssicherung zu verringern, da frühzeitig gewarnt werden kann, wann mit einer hohen Wahrscheinlichkeit Schlechtteile produziert werden. Für den Einsatz der KI wird die Datenerfassung an den Maschinen und das Vermessen von Teilen auf ein neues Level gehoben und so die digitale Transformation von HEISMANN Drehtechnik weiter unterstützt.
Ressourceneinsparungen durch den Einsatz Künstlicher Intelligenz
Durch die optimierte Prozessregulierung wird der Ausschuss verringert, wodurch in erster Linie Rohmaterialien, wie Stahl, Aluminium und Messing eingespart werden. Diese Einsparung beläuft sich voraussichtlich auf etwa 10.700 kg pro Jahr. Zusätzlich werden weitere Ressourcen, wie Strom (ca. 19.600 kWh pro Jahr), Kühlmittel, Zeit und Arbeitskraft, eingespart, da sie nicht für die unnötige Produktion fehlerhafter Teile aufgewendet werden müssen. Dies trägt schlussendlich zu einer signifikanten Verringerung des CO2-Ausstoßes bei. Zudem soll die Lebensdauer der Werkzeuge verlängert werden, was zur Verringerung von Stillständen der Maschinen und somit zu weiteren Einsparungen führt, da der Wiederanlauf von Maschinen die Anfälligkeit für die Produktion von Ausschuss erhöht.
Vorstellung des gemeinsamen KI-Pilotprojekts mit der Heismann Drehtechnik GmbH
- Martin Gawenda, Heismann Drehtechnik GmbH
- Johannes Solzbacher, Deutsches Forschungszentrum für Künstliche Intelligenz GmbH (DFKI)
Technologie
Fähigkeiten der KI: Datenanalyse, Handlungsempfehlungen geben
KI-Modelle: Regressionsmodelle, Random Forests, LSTMs, GRUs
Wertschöpfung
Phase: Produktion & Qualitätskontrolle
Ziel der KI: Erkennung von Fehlern zur Vermeidung von Ausschuss, Optimierung der Standzeiten
Ressourceneffizienz
Reduzierung der Fehlerquote um 20% und daraus resultierende Materialeinsparungen