KI-basierte Einsparungen von Werkzeugen im Fräsprozess
Der Standort Homburg der Robert Bosch GmbH fertigt unter anderem modernste Dieseltechnologien für Personen- und Nutzkraftwagen. Zudem wird dort sukzessive Kompetenz im Bereich Wasserstofftechnologie aufgebaut. Das Fräsen ist ein zentraler Prozess der damit verbundenen Metallverarbeitung. Eine große Herausforderung bei Fräsprozessen und der Produktion hoher Stückzahlen liegt in der Festlegung der Intervalle zur Auswechslung der Werkzeuge, um Qualitätsproblemen zu vermeiden. Durch eine KI-basierte Lösung soll die tatsächliche Abnutzung dieser Werkzeuge ermittelt und klassifiziert werden, um den optimalen Zeitpunkt für den Werkzeugwechsel zu bestimmen.
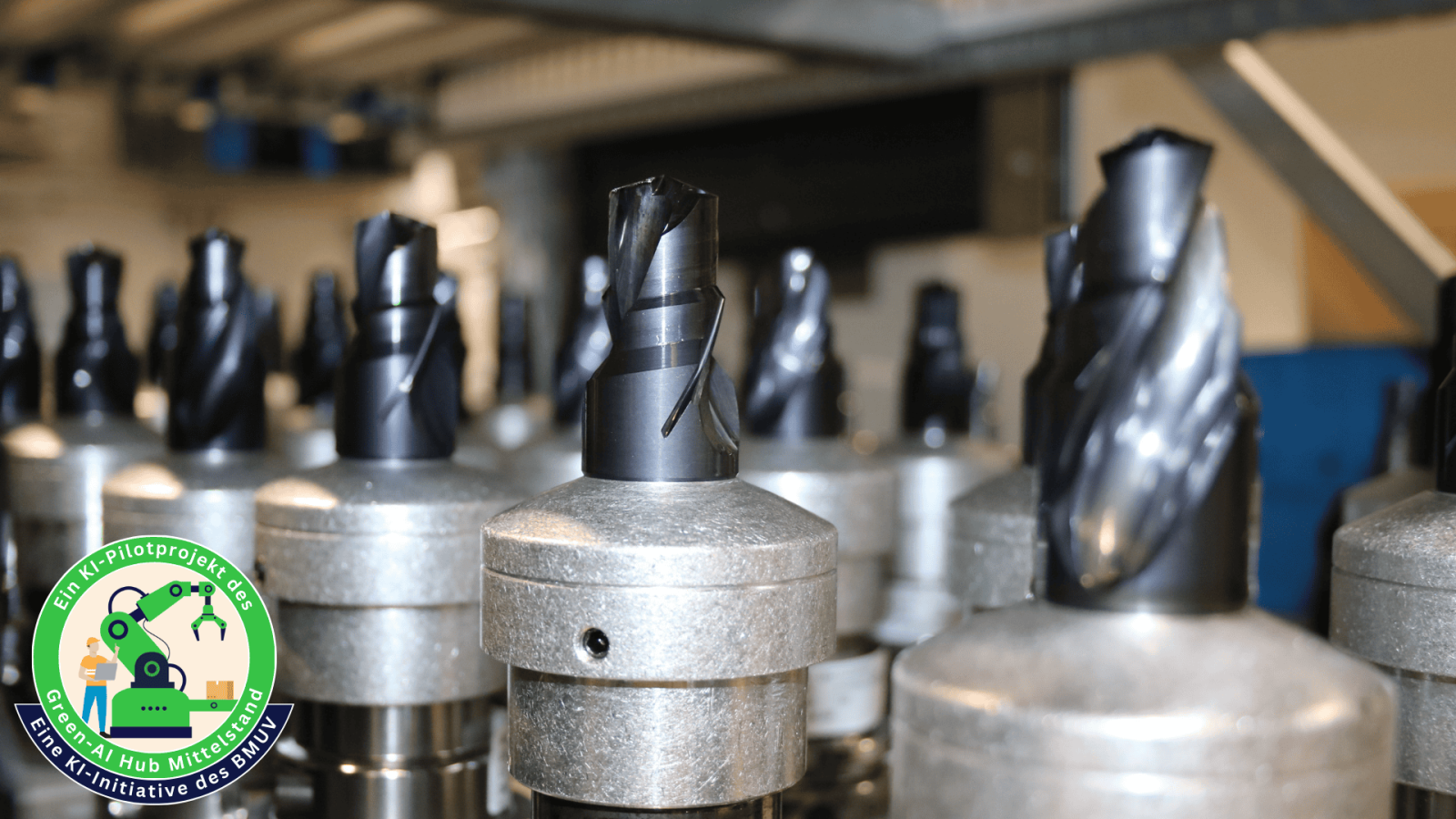
Ziel: Die Ermittlung der tatsächlichen Abnutzung von Werkzeugen, um diese optimal zu nutzen und den Verlust des Werkstücks durch Werkzeugbrüche zu vermeiden.
Umsetzung: Durch KI-Methoden aus dem Bereich des überwachten Lernens sowie die Datenverfügbarkeit im Unternehmen ermöglicht das Training eines KI-Modells, den Abnutzungsstand verschiedener Werkzeuge automatisiert zu ermitteln.
Effekt: Durch die Ermittlung der tatsächlichen Wechselintervalle eines jeden Werkzeugs wird die Nutzungsdauer der Werkzeuge erhöht und Werkzeugausfälle vermieden. Da die verwendeten Werkzeuge in der Herstellung einen hohen CO2-Fußabdruck hinterlassen, trägt der geringere Werkzeugverbrauch sowie die Vermeidung von Werkzeugbrüchen auch zum Klimaschutz bei.