AI-based optical quality assurance
Artificial intelligence (AI) at a traditional automotive supplier? The Green-AI Hub pilot project with KÖSTLER GmbH from Annaberg-Buchholz in Saxony shows that this is possible. Among other things, the company processes textiles for airbags. The quality control in the production process for these textiles is still done manually, which is monotonous and generates waste. With the help of AI, we are developing an automated quality inspection system for fabrics.
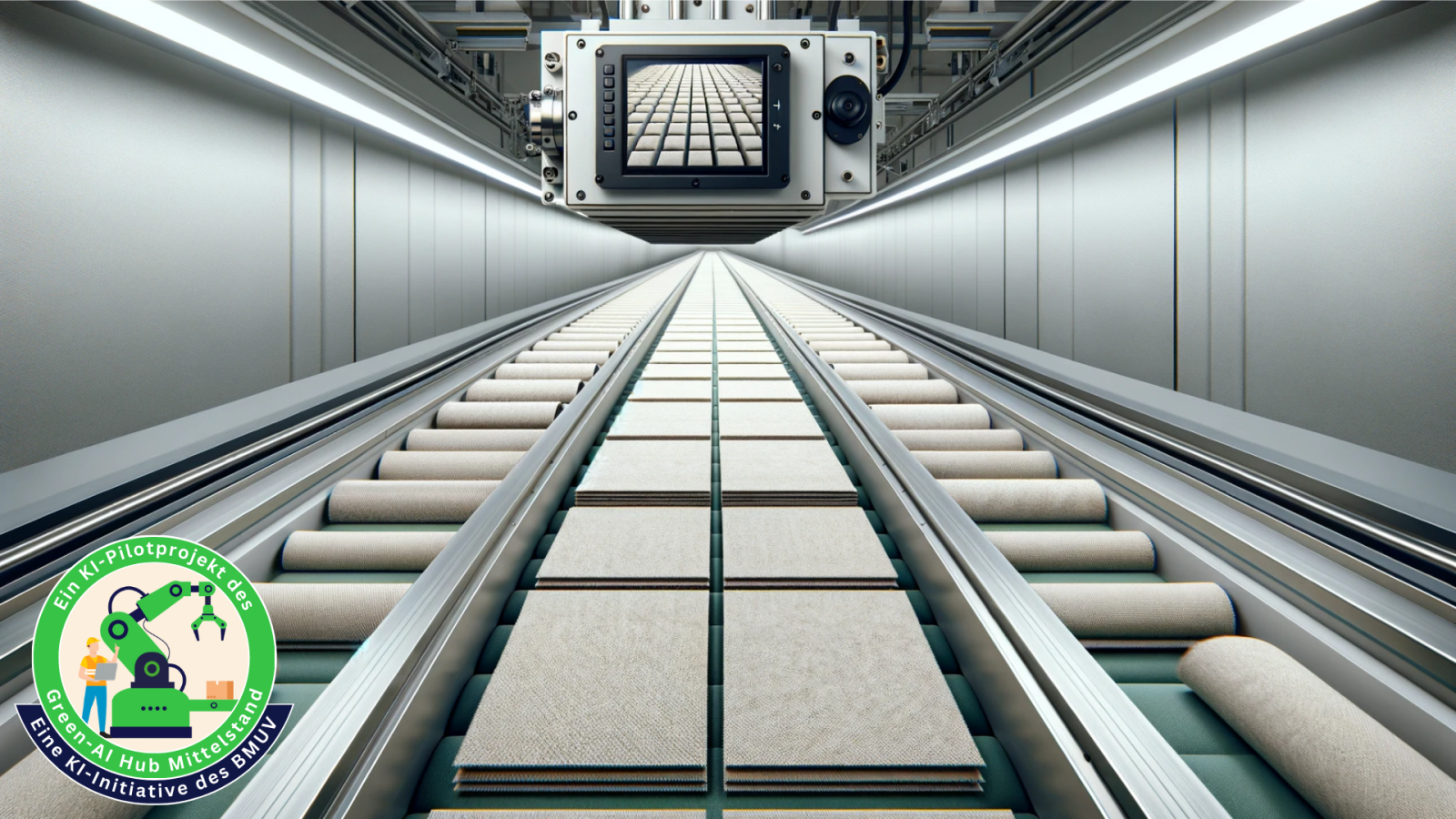
KÖSTLER GmbH: an automotive supplier with history
KÖSTLER is a family business founded in 1891 by Johann Köstler in Graslitz. Originally, the company was involved in the construction of musical instruments and accessories. After 1945, the company continued in Nauheim and expanded its business field to the automotive industry in 1963. With over 50 years of experience, KÖSTLER is now a leading manufacturer of airbag hinges made of textile fabric. The production sites are located in Annaberg-Buchholz and Chomutov, Czech Republic. KÖSTLER produces interior parts such as armrests and sun visors.
Challenge: increasing quality requirements
Like other medium-sized companies, KÖSTLER is also facing the challenge of a shortage of skilled labour. This makes it difficult to recruit qualified employees, which affects production capacities and innovation capabilities. At the same time, the demands for the automotive industry have increased considerably. End customers expect the highest quality, process reliability, and efficiency. As a result, there are increasingly stringent standards for the quality and reliability of products and services, such as those outlined in the IATF 16949 standards. In addition, there are growing expectations for sustainable and innovative materials, particularly in the area of lightweight construction. All of this requires constant adaptation as well as investments in personnel development and technological advances, including quality assurance.
KÖSTLER relies on a combination of traditional craftsmanship and modern production techniques. Many processes are done by hand, which guarantees a high level of precision and care. For example, textile nets are intricately sewn into hinges. This allows products to be very well adapted to specific customer requirements. After completion, the hinges are sold and processed in further production steps, for example through injection moulding into plastic parts. This process allows the textile hinges to be integrated into complex components used in the automotive industry and other sectors.
Improved quality assurance through artificial intelligence
The AI pilot project with KÖSTLER focuses on using AI for quality assurance of the cut textile nets. For this purpose, an innovative inspection station is being developed that automatically sorts the textiles into good and bad according to the requirements.
The inspection station uses AI-supported image processing and machine learning to precisely evaluate the textiles. Automated sorting ensures high product quality and reduces defective parts.
This also relieves employees from monotonous work and allows them to focus on more demanding tasks, as fewer staff would be required for quality control. The AI-supported inspection station improves production efficiency and quality. In the long term, this strengthens the company's competitiveness and supports sustainable growth.
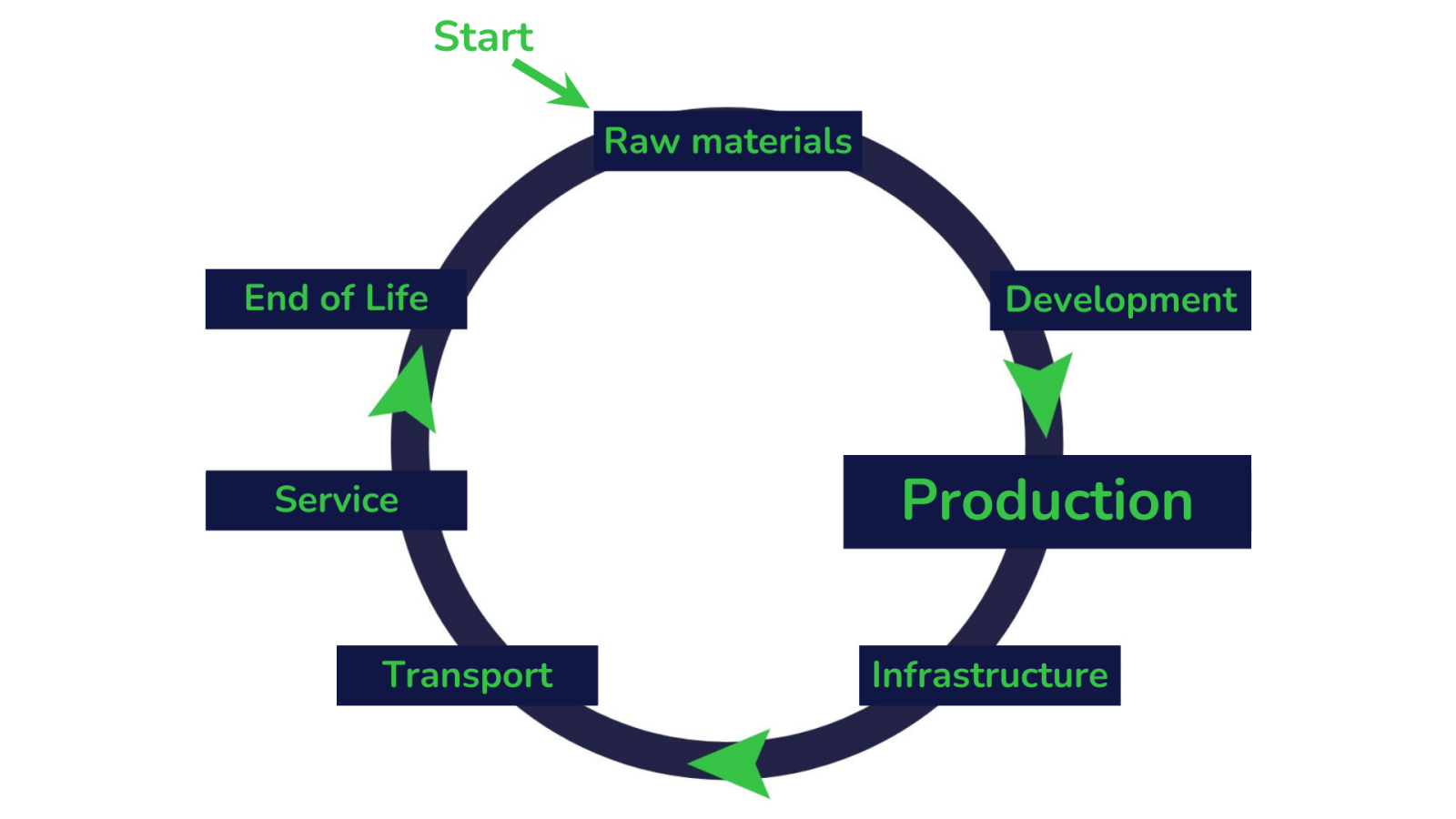
Resource efficiency through AI
Through the AI pilot project with the Green-AI Hub Mittelstand, KÖSTLER is using AI to increase resource efficiency and achieve significant savings. AI-based quality inspection is more precise and consistent than human quality inspection. This is expected to reduce the reject rate.
Another advantage is the early detection of error trends. Through continuous monitoring and analysis of production data, AI program can quickly identify deviations and patterns, enabling immediate corrections to be made when cutting the textile nets.
Currently, two templates made of plastic and metal are produced per design for quality inspection. By implementing the AI-supported inspection station, the need for these templates can be reduced by 50 percent to just one percent.
In addition, the space and heating requirements of the large rooms currently used for manual quality control will be reduced. The automated inspection station requires less space and energy, which reduces operation costs and further increases resource efficiency.
Presentation of the Green-AI Hub pilot project “AI-based optical quality assurance“ - 5:38 min.
-
Sven Pultar, German Research Center for Artificial Intelligence GmbH
Technology
AI capability: data analysis and image recognition
AI model: AI-supported image processing and machine learning
Value creation
Phase: Quality control
Aim of AI: Automation of manual quality inspection processes
Resource efficiency
Lower reject rate and savings in operation costs and production materials