AI-supported 3D printing of orthopaedic insoles
The traditional production of orthopaedic insoles requires the use of various frameworks and is very time consuming. Johann Herges GmbH, a third-generation shoe manufacturer, is striving to fundamentally transform the production of orthopaedic insoles using artificial intelligence. The company plans to use an AI-supported 3D printing process to produce orthopaedic insoles to increase resource efficiency. The pilot project is investigating which advanced machine learning models, such as artificial neural networks (ANN) and support vector machines (SVM), are best suited for this process.
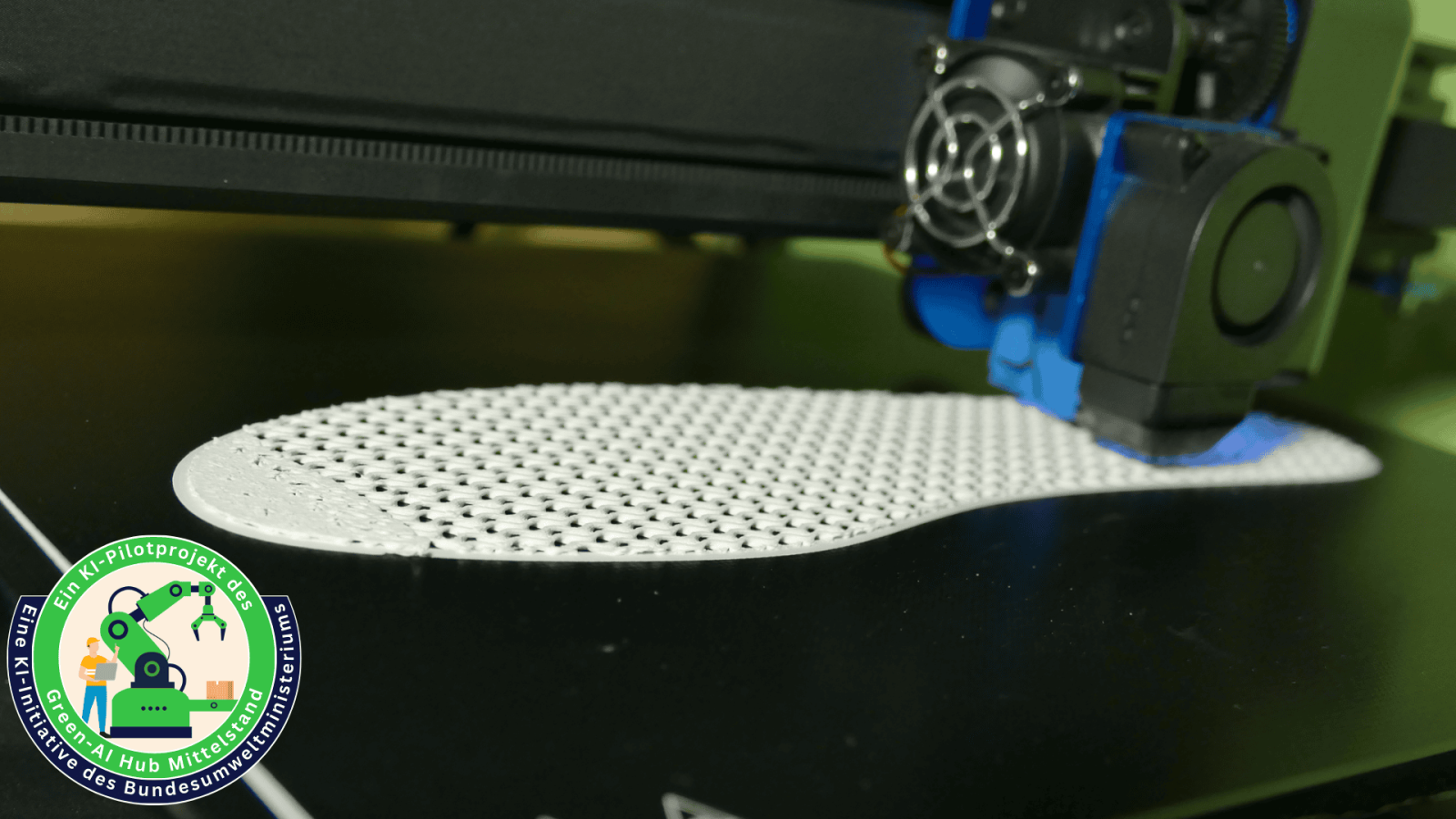
Innovative production of orthopaedic insoles made in Saarbrücken
The Johann Herges GmbH is an innovative shoe manufacturer that produces a wide range of orthopaedic solutions. This includes custom-made shoes, orthopaedic custom-made shoes, compression stockings, bandages, orthoses, and especially orthopaedic insoles, which address a wide range of disease patterns. The orthopaedic insoles are traditionally manufactured using footprints in foot foam. Materials are then glued onto unfinished blanks and sanded.
Challenge: replacing the subtractive production process
Depending on the disease patterns, building insoles using blanks can be very time consuming or even completely impossible. In around 30 percent of cases, a subtractive process is therefore used, in which insoles are made from blocks of ethylene vinyl acetate (EVA), a petroleum-based product. However, about 80 percent of the material used in the milling process is lost as waste. Therefore, an alternative solution is 3D printing of insoles, which produces virtually no waste. Nevertheless, the extensive manual design process often stands in the way of an economical application.
Additive production process through AI-supported 3D printing
3D printing offers a sustainable alternative that uses less material. A printable 3D model differs significantly from a model designed for conventional milling. With a 3D-printed model, filling structures must be used to create different stiffnesses within the insole. However, the manual construction of these filling structures is time consuming. This is where AI comes into play by automating the process. Using pressure measurements, the AI analyses the foot and generates a 3D model with optimal filling structures. As part of the pilot project, the company plans to use advanced machine learning models such as artificial neural networks (ANN) and support vector machines (SVM). The goal is to determine which model is best suited for the process. A training dataset will be created to ensure that the unique expertise and know-how of the orthopaedic technicians are integrated into the automatically generated model. In the beginning, a powerful computer system may be required once for this step. However, in later use and in the daily workflow this should be possible with a standard PC without any problems.
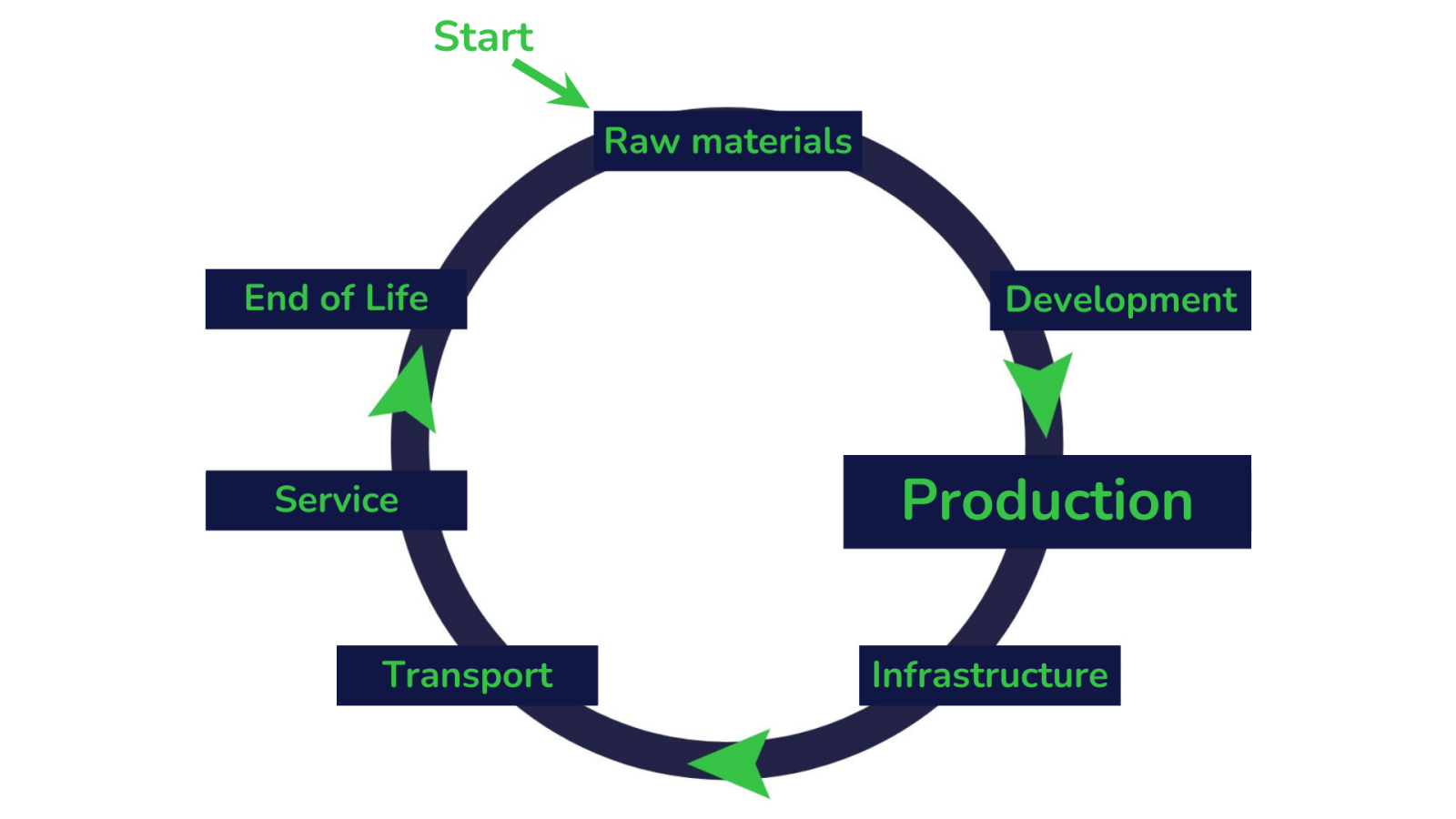
Resource efficiency through AI-based production conversion
The project addresses the “production” section of the value chain. AI significantly simplifies the processes involved in the production of complex insoles. Numerous time consuming manual steps are a thing of the past, as the insoles are now built using 3D printing. Manual work is limited to recording the foot characteristics and making minor adjustments before 3D printing. Overall, this results in a more efficient use of human labour, while the unique expertise and quality that sets the company apart is still maintained in every insole produced through training the AI with manually created data sets.
Integrating AI has had a transformative effect on the company's resource efficiency. Transitioning from a subtractive to an additive manufacturing method has resulted in a significant reduction of material consumption. Material savings of over 70 percent have been recorded for plastics, particularly ethylene vinyl acetate (EVA). In addition, the 3D printing process is up to 60 percent more energy efficient than milling. These developments suggest that a reduction in the use of materials will lead directly to a lower carbon footprint. While the integration of AI requires initial investment in technology, training, and integration, these costs are quickly regained as significant savings in materials and energy are achieved.
Via the link you will find an RTL report in the Nachtjournal from 31.05.2024 (from minute 27:35) on artificial intelligence, in which the Johann Herges GmbH is mentioned.
Presentation of the Green-AI Hub pilot project “AI-supported 3D printing of orthopaedic insoles“ - 14:12 min.
- Johannes Herges, Johann Herges GmbH
- Felix Kosmalla, German Research Center for Artificial Intelligence GmbH
Technology
AI capability: generation of a 3D model
AI model: regression, digital models, artificial neural networks (ANN) and support vector machines (SVM)
Value creation
Phase: production
Aim of AI: additive production process through AI-supported 3D printing
Resource efficiency
Savings on materials: over 70 percent
Energy savings: up to 60 percent
GHG reduction potential of 0.63 t CO2e
Unternehmen
Industry: Manufacturing industry, Shoe manufacture, Orthopaedic shoe technology