AI-controlled tool optimisation
Plastic waste such as packaging can be used for energy recycling as a substitute for fossil fuels or reused as plastic recyclate in new products. This is the goal pursued by BBM Maschinenbau und Vertrieb GmbH. The company manufactures equipment for the production of plastic products. By simulating the production process using a digital twin and subsequent AI-controlled tool optimisation, the company has been able to increase the proportion of recyclate used to as much as 80%.
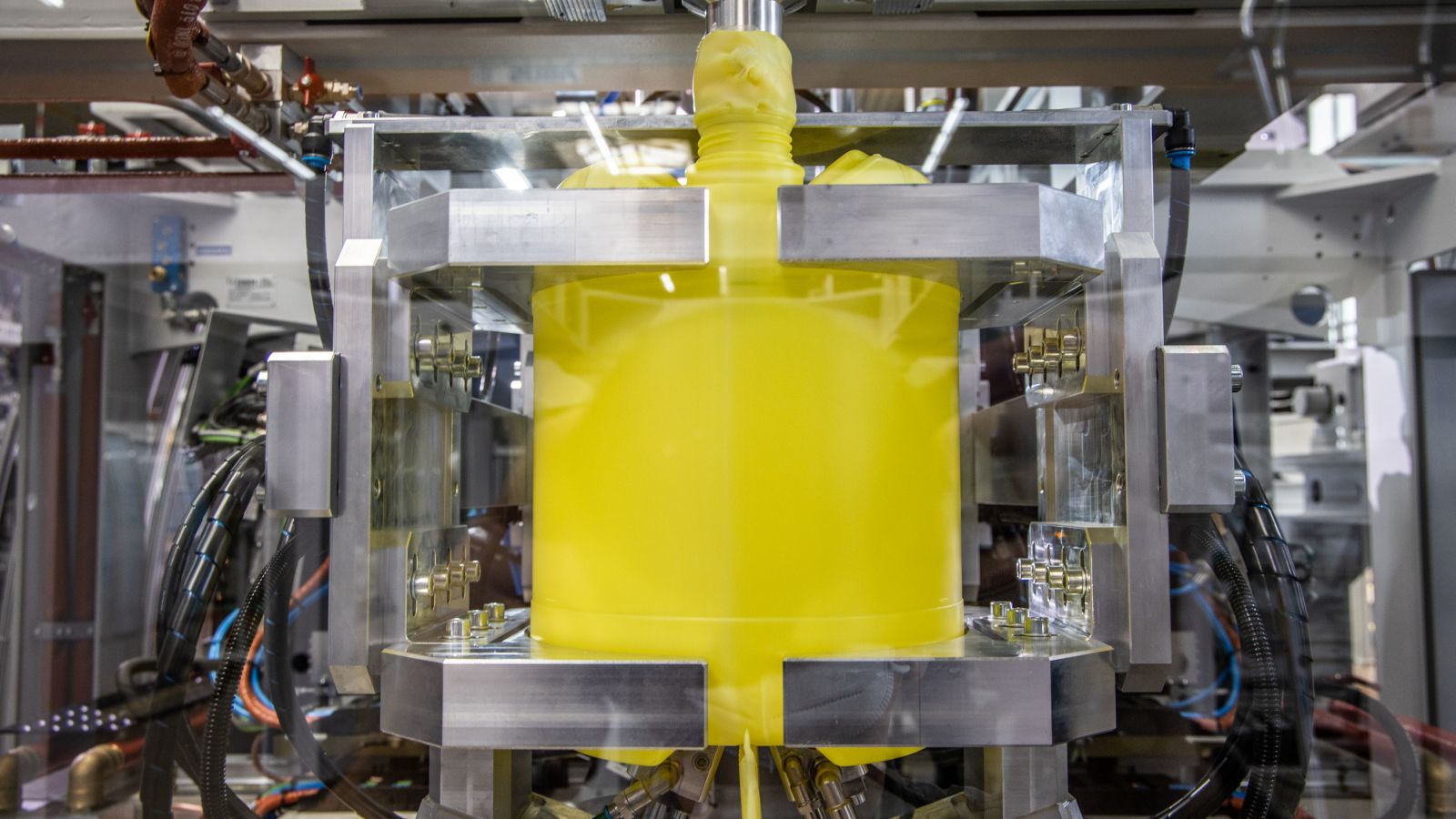
AI-controlled tool optimisation
BBM Maschinenbau und Vertrieb GmbH, based in Langenberg, Westphalia, produces equipment for the manufacture of hollow plastic bodies such as drums, canisters and accessories for the automotive industry. For this purpose, the company already relies on the use of recycled material. The shredded material comes from waste, which is why the quality varies greatly due to the diversity of its previous use. For this reason, the material is difficult to control and proves difficult to process. In drum production, for example, the primary and secondary material flows into the plant via various extruders and is combined in a so-called spiral distributor.
Evolutionary AI process
To optimise this process, the company called in Ianus Simulation GmbH, which created a digital twin of the spiral mandrel distributor. Artificial intelligence can then be used to select the optimum spiral mandrel distributor. The principle is simple and based on the evolutionary process from nature: first, the artificially intelligent software designs different spiral mandrel manifolds, with different parameters such as heights, gradient, etc. This is used to generate thousands of variants (individuals), each of which is used to simulate the production process. The intelligent software then determines which design allows as much recyclate as possible to be used while maintaining the same quality requirements. The best 30% of the first generation are selected and examined for regularities, which are then incorporated into the formation of new digital twins – until an optimum spiral mandrel distributor has been identified after about ten generations.
Recycled content and service life increased
With the aid of AI, a recycled content of around 80% was achieved in barrel production. The inner and outer coating only account for a share of 10% each. At the same time, thanks to the simulation, it was possible to significantly increase the quality and service life of the products and increasingly close the material cycle.
BM Maschinenbau und Vertrieb GmbH
... produces equipment for hollow plastic parts such as drums, canisters and accessories for the automotive industry. With the help of the use of AI, the company has been able to achieve a recycled content of around 80% in barrel production. The inner and outer coating only account for a share of ten percent each. At the same time, thanks to the simulation, it was possible to significantly increase the quality and service life of the products and increasingly close the material cycle.
Process optimisation with AI
BBM Maschinenbau und Vertrieb GmbH and IANUS Simulation GmbH reduce the resources used in the production of hollow plastic parts. This is achieved with the help of digital twins. Here they explain exactly how (video in German only):
Technology
AI capability: act, understand
AI model: evolutionary algorithms or reinforcement learning
Value creation
Phase: development
Aim of AI: optimisation of the spiral mandrel distributor
Resource efficiency
Material savings by increasing the recycled content to 80%.
Qualitatively durable drums & tools