Vollautomatisches Warehouse Management
Wie lässt sich die interne Logistik an einem komplexen Produktionsstandort hinsichtlich der Ressourceneffizienz optimieren? Diese Frage hat sich die Blechwarenfabrik Limburg GmbH bei der Planung und dem Bau Ihres neuen Produktionsstandortes in Limburg gestellt. Um hier einen reibungslosen Ablauf zu gewährleisten, steuert nun eine KI den internen Warentransport und das Lagersystem.
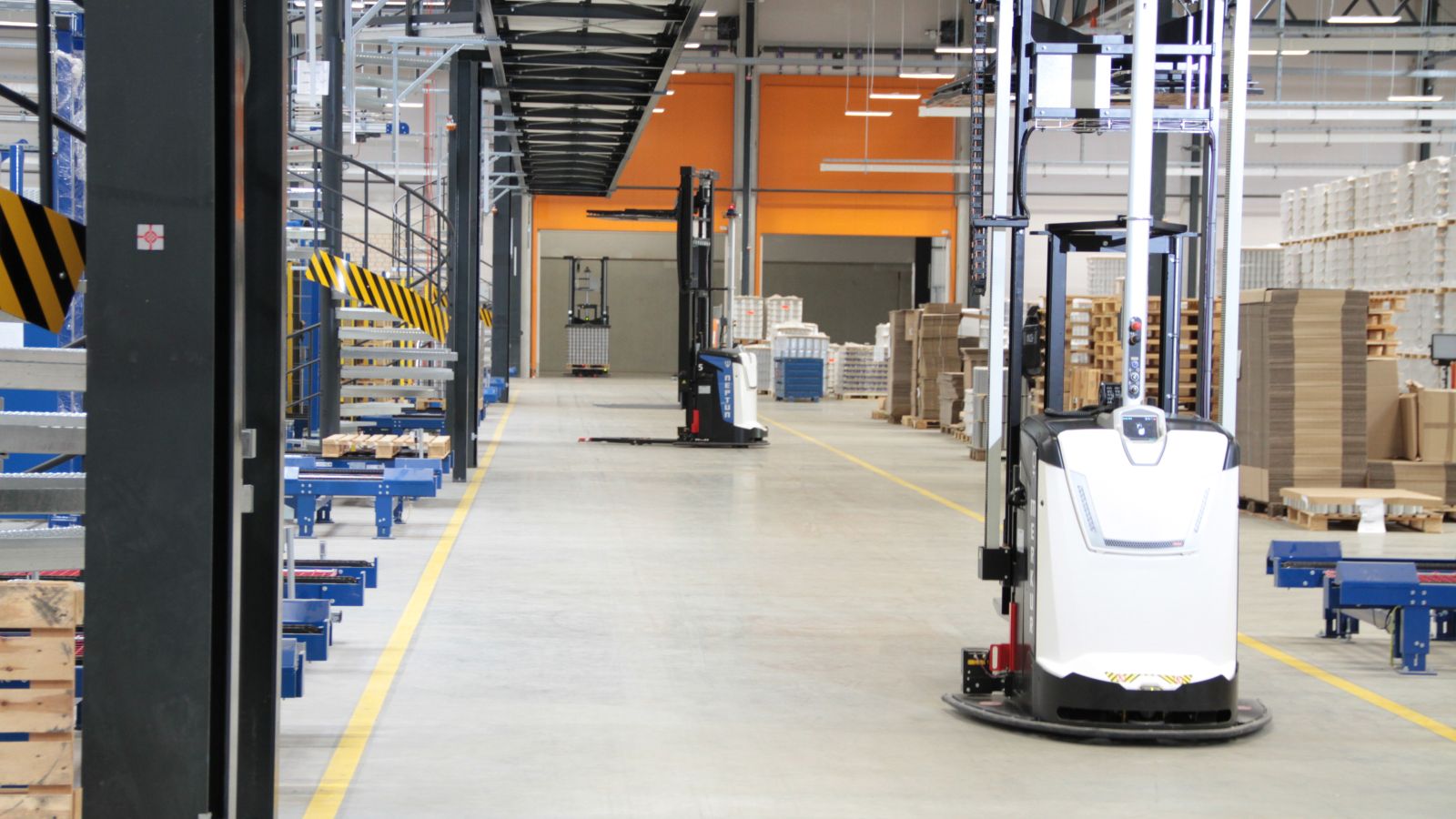
Vollautomatisches Warehouse Management
Bewegten zuvor manuell gesteuerte Gabelstapler die Materialien und Waren zwischen Lagern und Produktionslinien, werden diese nun vollautomatisiert von fahrerlosen Transportfahrzeugen durch die Produktionshalle befördert. Ohne menschliche Bedienung fahren diese durch das Gebäude und versorgen die Produktion mit den benötigten Materialien.
Auch für den Abtransport wird zum passenden Zeitpunkt ein Transportfahrzeug bereitgestellt, welches am Ende der Produktionslinie von einem Palettierroboter mit der Fertigware bestückt wird. Anschließend fährt das Transportfahrzeug entweder zum Warenausgang oder in das ebenfalls vollautomatisierte Hochregallager, wo ein fahrerloses Regalbediengerät die Fertigwaren in das Lager einsortiert. Dabei werden die Waren keinem vordefinierten Standort zugewiesen, sondern von außen betrachtet zufällig verteilt. Allerdings fokussiert sich die KI-gestützte Sortierung auf den verfügbaren Platz und die Minimierung der Fahrtwege. Die Lagerplätze der Fertigwaren werden in einer Datenbank gespeichert.
KI-gestütztes Warehouse Management System
Möglich wird diese vollautomatisierte Steuerung der internen Logistik durch die erfolgreiche Implementierung eines vollumfänglichen Warehouse Management System (WMS). Das KI-gestützte System weiß zu jedem Zeitpunkt, wo sich die Rohmaterialien, die Fertigwaren und die Transportfahrzeuge befinden und an welcher Stelle diese benötigt werden. So kann der Materialfluss möglichst Zeit- und Energieeffizient gesteuert werden.
Opimierte Prozesse - 100 t Weißblech pro Jahr eingespart
Durch Umstellung auf vollautomatische Transporte und Lagerung konnte zum einen die Lieferbarkeit gesteigert und zum anderen der Ausschuss reduziert werden. Das Verringern von Transportschäden führte, in Kombination mit allen weiteren optimierten Prozessen des neuen Standorts, zu einer Einsparung von ca. 100 t Weißblech pro Jahr. Zudem wird durch die Automatisierung die Unfallgefahr durch menschliches Versagen auf ein Minimum reduziert.
VDI Zentrum Ressourceneffizienz (2021): Potenziale der schwachen künstlichen Intelligenz für die betriebliche Ressourceneffizienz, Studie, VDI Zentrum Ressourceneffizienz GmbH, Berlin.
Die Blechwarenfabrik Limburg GmbH
Als einer der ältesten Stahlverpackungshersteller in Deutschland produziert das Unternehmen mit ca. 400 Mitarbeiter*innen an vier internationalen Standorten Verpackungen für chemisch-technische Füllgüter wie Farben, Lacke und Lasuren. Allein in Deutschland werden über 24.000 Tonnen Weißblech pro Jahr zu über 100 Behälter-Variationen verarbeitet. Um hier einen reibungslosen Ablauf zu gewährleisten, steuert nun eine KI den internen Warentransport und das Lagersystem.
Technologie
Fähigkeit der KI: handeln, verstehen
KI-Modell: Robotik und Optimierungsproblem
Wertschöpfung
Phase: Produktion & Intralogistik
Ziel der KI: Optimierung der internen Logistik
Ressourceneffizienz
Materialeinsparung: ca. 100 t Weißblech pro Jahr
Einsparungen von fast einer halben Million Euro an Material- und Energiekosten pro Jahr
Reduzierung von Transportschäden